The counterfeiting gangrene is not a recently discovered disease. It already infected the watchmaking industry during the 18th century. To protect itself from the usurpation of the already prestigious Genevan origin, the corporation of watchmakers in this era created the Hallmark of Geneva (H.o.G).
Since the commercial law did not really exist at this time, in order to mark their difference, the leaders of the Genevan watchmaking chose to increase the quality of their production.
The "Hallmark of Geneva" was born. Its quality requirements were difficult enough to differentiate a mere imitation from a watch made in the Canton after the Poinçon's criteria.
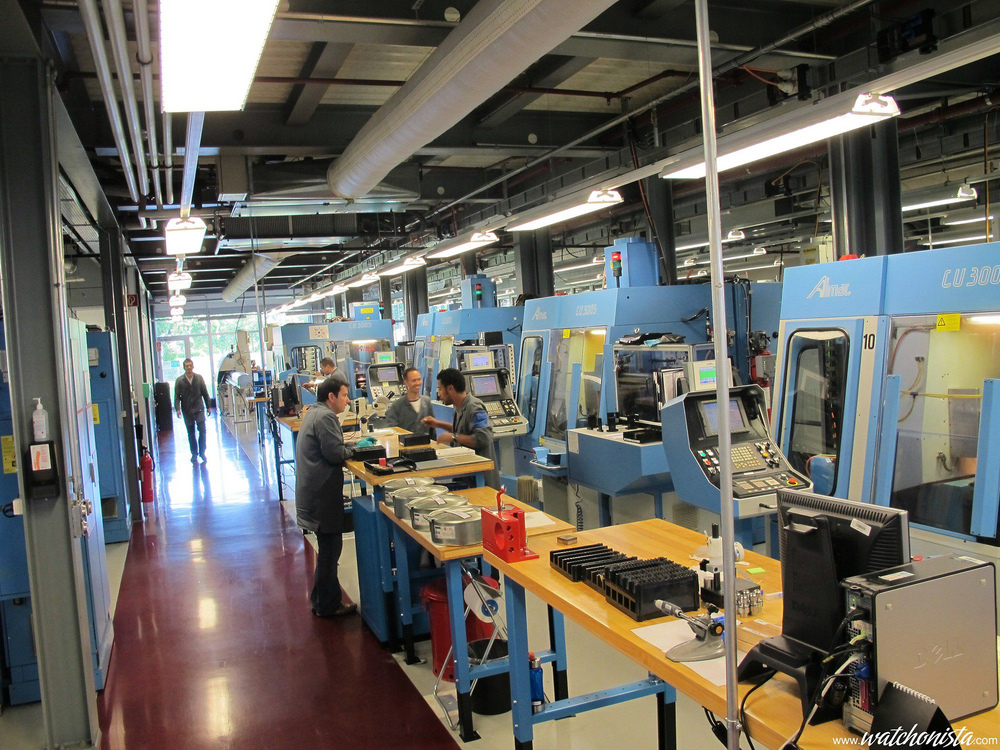
In 2011, these criteria were extended to the entire watch. The Hallmark is difficult to obtain, because it mainly involves the hidden parts of a watch. That implies investing lots of energy into components that only a technician will be able to admire, for example during a maintenance operation.
The Hallmark mainly regards the finishes: all the components must be devoid of cutting marks, and all of them must feature a finish such as stippling, drawing, and most of all polishing. This work also guarantees a better durability of the components.
If the aesthetic aspect is crucial, now the Hallmark of Geneva has also four performance requirements: Waterproofing, accuracy, additional functions as well as a power-reserve tested in conditions as close as possible as when the time-keeper is worn by customers. The chronometric precision tests are done by comparing photos, shot on a seven-day cycle; the gap observed after this period should not exceed one minute.
In 2011, the Swiss watchmaking industry produced 29.8 million pieces. Only one million was COSC certified (by Timelab, which also manages the Hallmark) and 25,000 were granted the Hallmark of Geneva. Amongst theses 25,000 watches, 5000 were produced by Roger Dubuis, that is to say the entire production of the brand.
Thus, the Roger Dubuis Manufactory is unique in many respects.
Most of the manufactories of the Canton of Geneva are located in horologic-industrial sites at Meyrin or at Plan-Les-Ouates. Almost all of these manufactories have at least one facility located in the Vallée of Joux or at the Chaux-de-Fond; these sites produce the "chips", which are assembled and sometimes finished in the Canton of Geneva.

But Roger Dubuis goes far beyond the affiliation of the Genevan area: 95% of the components are produced on the first floor of the Meyrin building. The only parts that are produced elsewhere are the rubies, the sapphire crystals and the titanium watchcases, whose machining leads to fire hazards difficult to manage, in a non-specialized Manufactory.
One of the unforeseen consequences when the factory opened, in 1995, is that the brand probably has the smallest per watch CO2 footprint: actually, as every piece is transformed and finished in a single building, one avoids the endless back-and-forth between diverse subcontractors' facilities.
If the company was created in 1995, it only granted itself the title of Manufactory in 2000. The old fashioned or even knightly approach (which legitimizes the "Excalibur" series) was to integrate all the watch creation steps before claiming to be a Manufactory. At Geneva, one is used to be quicker: to grant oneself the title of "Manufactory", one generally waits to be able to print home-made press kits.
When every workshop started operating, it developed horizontally to fill the orders. When one knows how the Swiss manufactories usually grow, that is to say, in a far more opportunistic way, one can be surprised by Roger Dubuis' choices. But the watchmaker, during this period accompanied by Carlos Dias, had a real industrial and horologic vision, the choice of building the foundation first was indisputably logical.

Personally, I already knew some highly integrated factories with limited production (RD currently produces less than 5000 watches per year), such as De Bethune… But the integration level of the Roger Dubuis production, together with the Hallmark of Geneva is unique. And the obsession for the "home-made" goes very far because every single component, from the rarest, the hairspring, to the most common, the screw, is transformed and finished in the same facility.

But when you enter the first floor of the Meyrin building, the most impressive is that you come face to face with automatic lathes. It is true that at first sight, a lathe is not really sexy (or at least far less than some finishers).
But even the most prestigious manufactories usually subcontract their screws to houses such as Affolter... The lathing process is generally associated with the making of wheels. It is an excellent way to guarantee an optimal reactivity during the production of these types of components, for example to adapt the dimensions for the polishing process.



The wheels, the pinions and the screws will undergo systematic finishing processes (almost always polishing). In the diverse workshops, each finisher is specialized in one category of components.
For example, to finish the wheel teeth, one utilizes discs made of diverse woods, such as pear, beech wood, boxwood...The "mill" is slightly off centered with a piece of wood (usually a toothpick) , resulting in the elliptical movement of an endless screw, in order to alternatively pass between the teeth of every wheel;
The type of wood and the thickness of the "off-centering piece" depend on the kind of wheels to be polished. The polishing process in itself is pretty quick (between 3 and 15 seconds), but the protection and the storage of wheels takes most of the time invested in the procedure.
So, the pinions are produced in the adjoining workshop. For example, the polishing of a wheel's pinions takes 17 different operations, performed by the same operator.
Therefore, the technician must switch machines and tune them accordingly, as many times as necessary.
Considering the tiny scale of these components, it is an ant's work, literally.

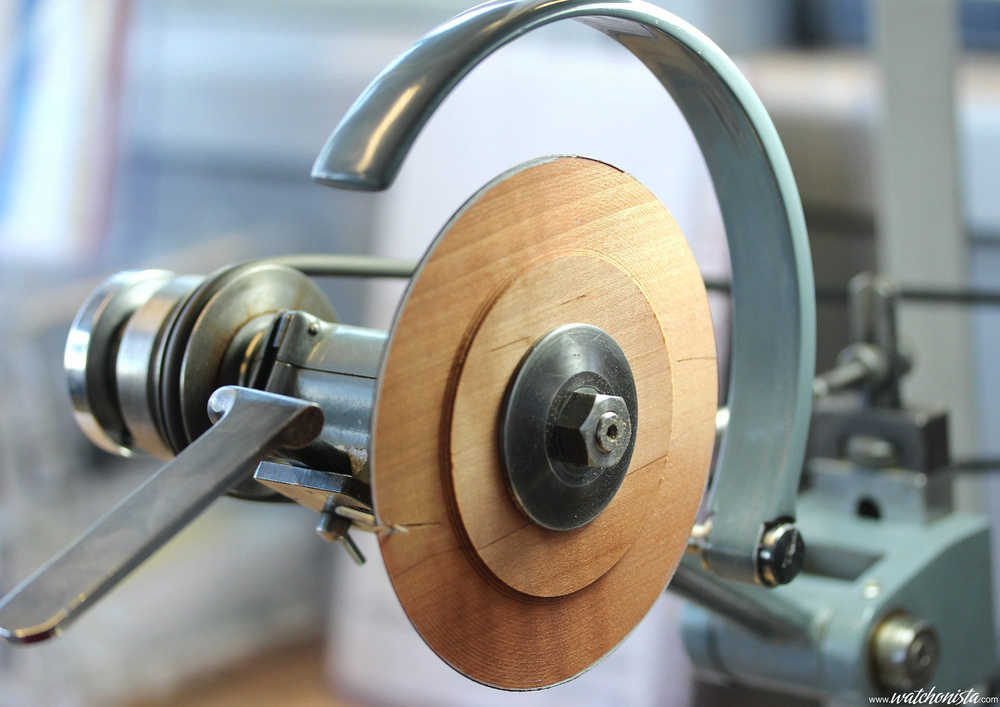


The other main activity of Roger Dubuis Manufactory's first floor is the cutting of the bridges and plates.
The cutting processes are quite common and are generally performed on brass blocks.
One of Roger Dubuis' specialties is the magnificent skeletons, especially that of the double tourbillon with differential gear. At RD's, the skeletons are directly executed by numerical control machines; Therefore, all the mechanical stresses are pre-calculated, which prevents the warping of the weak plates.
In a similar way, the decorations of these components are machined, notably with a digital engine-turning machine;
Indeed, machines are more dependable in their motions and more economical in their material savings, a valuable quality regarding the stability of skeletonized parts.



As for the classic bridges and plates, they systematically go through the so-called "Hallmark of Geneva" workshop. It is one of the most active departments of the Manufactory: several dozens of finishers work at making all the movement's components beautiful. The techniques are quite common: engine-turning, Geneva stripes, polishing (with "beer-mug coaster" shaped discs). The obsessional pursuit of the good- workmanship and its systematic application is always as impressive as ever.




The last noteworthy part of the first level is the prototyping workshop. The prototype makers have a freehand to follow the creators' blueprints, with several independent numerical control machines as well as all the tools required for the finishing steps and the basic assembling processes;
They are totally independent regarding the fabrication of the prototypes. Therefore, the overall activities are not hindered and the reactivity and the confidentiality are optimal.

Then, we have the opportunity to take a tour of the core of the Manufactory (metaphorically as well a physically: the workshop sits at the very middle of the building), when we enter the workshop where the escapement devices are assembled. Unfortunately, the door to the shop, where the Elinvar blocs are transformed into hairsprings, remains closed. However, the watchmakers who built the escapement devices confide in us a few secrets.
Today, Roger Dubuis utilizes two families of hairsprings: the small one for the movements set at 28.800v/h and the bigger ones set at 21.600v/h, for the tourbillons. The assembling of the escapement device is the most strategic process in the fabrication of a Roger Dubuis watch. Indeed, each layout is modular and allows to easily assemble/disassemble the escapement device in a single step. The whole delicate tuning phase is performed in this workshop. The technicians have an unimaginable level of qualification and the communication with the workshop which produces the hairsprings could not be more direct: only one door separates them. The half dozen of technicians produce only 25 devices a day, two hours per escapement, actually. First of all, the hairsprings are cut out and set with a collet; then, the balance and the other components are fitted. An escapement device is composed of about 60 parts...





This enormous upstream work is useful, because it makes the work of the watchmakers and of the services department a lot easier. For this kind of result:
Excalibur double-flying tourbillon:

Excalibur minute repeater and tourbillon

Monégasque Tourbillon
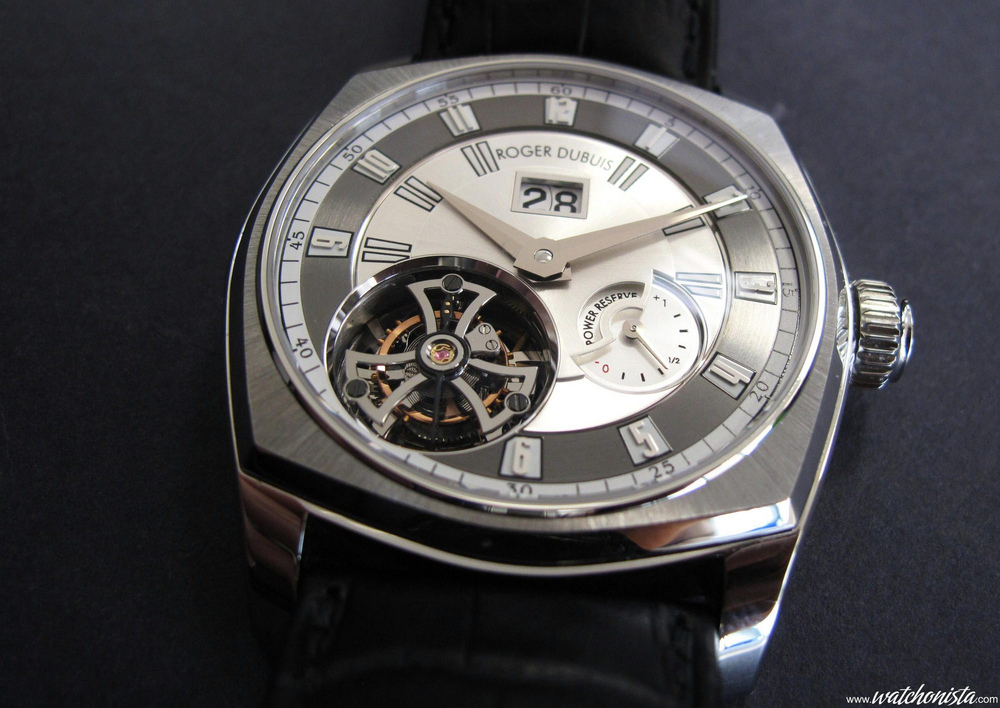
Excalibur 42

Velvet

Pulsion Chronograph

Monégasque Club

Throughout the multiple manufactories I have visited throughout the past few years, I had never noticed such a demonstration of strength, such a pursuit of quality.
If some very fine houses have as much savoir-faire as Roger Dubuis (but not more), these competencies are most often spread across several towns. In this case it is astounding: a single Genevan site integrates all of the crafts and machines required to produce a fine-watchmaking piece. All in all, the Hallmark of Geneva is only a consequence.